Bearings and Lubrication to Maintenance Bearings
- Share
- Issue Time
- Jun 21,2018
Summary
Bearings and lubrication, when the bearing is working, there must be sufficient lubrication. It is in order to ensure the effective.
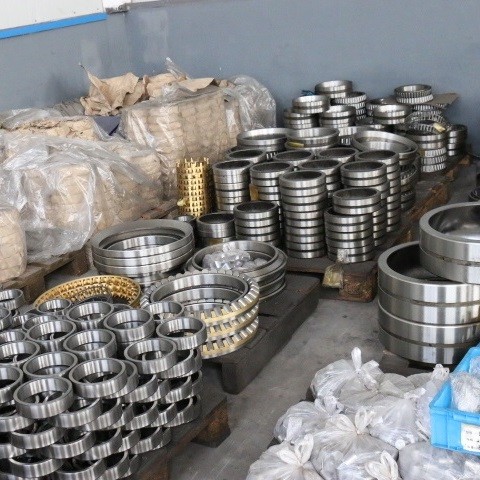
Bearings and Lubrication to Maintenance Bearings
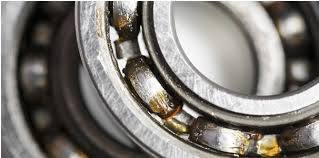
Packing
Some bearings use a thick grease for lubrication, push it into the gaps between the bearing surfaces, also known as packing. Hold the grease in place by a plastic, leather, or rubber gasket that covers the inside and outside edges of the bearing race to keep the grease from escaping.
Bearings may also be packed with other materials. Historically, the wheels on railroad cars used sleeve bearings packed with waste or lose scraps of cotton or wool fiber soaked in oil. Then later used solid pads of cotton.
Ring oiler
Splash lubrication
Pressure lubrication
For high speed and high power machines, a loss of lubricant can result in rapid bearing heating and damage due to friction. Also in dirty environments, the oil can become contaminated with dust or debris that increases friction. In these applications, a fresh supply of lubricant can be continuously supplied to the bearing and all other contact surfaces, and the excess can be collected for filtration, cooling, and possibly reuse.
Pressure oil
People commonly use pressure oiling in large and complex internal combustion engines in parts of the engine. Because the directly splashed oil can not reach there, such as up into overhead-valve assemblies. Highspeed turbochargers also typically require a pressurized oil system to cool the bearings and keep them from burning up due to the heat from the turbine.