What Causes Bearing Wear and How to Prevent [Quick]
- Share
- Issue Time
- Aug 3,2020
Summary
Bearing material wear obviously means the gradual reduction of material. There will be some very slight wear during the trial operation stage.
![What Causes Bearing Wear and How to Prevent [Quick]](https://icdn.tradew.com/file/201804/1572758/png/7389219.png?x-oss-process=image/quality,Q_90)
What Causes Bearing Wear and How to Prevent [Quick]
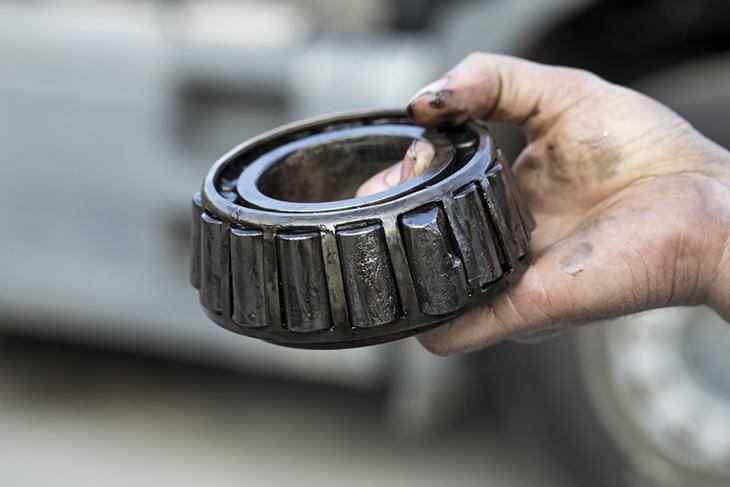
Bearing abrasive wear
◆Insufficient lubrication
◆The entry of dirt particles
◆Dark surface (mostly)
◆Process catalysis
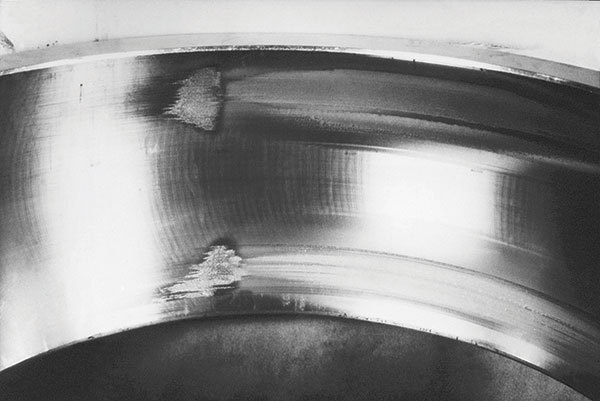
Bearing material wear obviously means the gradual reduction of material. There will be some very slight wear during the trial operation stage, most of which are just showing the track. When real wear occurs, most of it is due to insufficient lubrication or dust particles entering.
Usually, the surface features are dim. (Sometimes, the wear particles may act as a polishing material, and the surface may become very shiny, and all of this Depending on the size, hardness, and stage of the particles) This is an accelerated process because the wear particles will further reduce the possibility of lubricant and destroy the microscopic geometry of the bearing.
Polishing wear
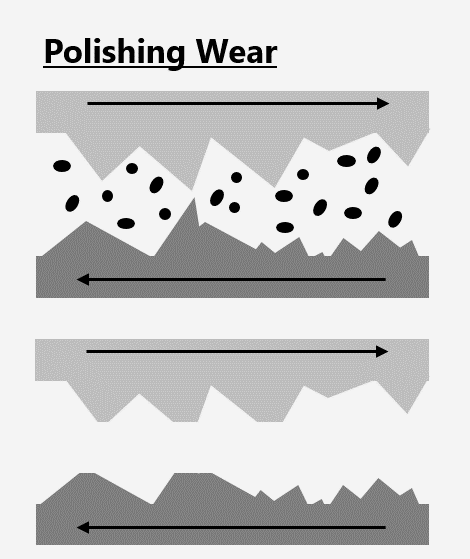
The raceway surface of the new bearing is shiny, but not very reflective (mirror). Therefore, the true mirror surface in the bearing means that something, sometimes called polishing, happens during the operation.
The most common explanation for the mirror raceway surface of rolling bearings is poor bearing lubrication, which usually means a thin oil film. This allows for metal-to-metal contact, causing wear and plastic deformation of the surface asperities. As long as the wear and plastic deformation of the surface is relatively light, that is, the "treatment" of the surface is only on the surface. Then a mirror surface is advantageous. If the overflight refrigerant invades the product channel, is it polishing wear or abrasive wear?
Sometimes, people combine the mirror surface with heavier wear, as shown in the picture above. The question is: How can the surface wear a millimeter and still look like a mirror? The explanation is that although the first polishing effect improves the surface roughness, the surface does not Form an oil film. Crude oil viscosity is too low and contains a lot of fine abrasive contaminants (superfinishing).
I
f the bearing has continuous polishing wear. These tiny particles are always present in the lubricant, but not every bearing with a thin oil film has polishing. Why is this? Suppose there are other factors that affect the start of the polishing and wear processes, such as a certain combination of low speed, heavy load, and thin oil film. The best way to avoid this abrasive polishing wear is to increase the thickness of the oil film.
More abrasive wear
Abrasives can cause rapid wear of rolling elements and rings, which can be observed on the outer ring of spherical roller bearings. You can see the depth of wear.
One area is severely worn, and then the inner ring is loosened and displaced (creep traces), leading to wear in the second area.
The cage is usually a key component of the bearing. The inner ring and rolling parts are hardened to about 60HRC. Most of the stamped retainers are made of unhardened mild steel. If lubrication fails, the cage may be the first component to fail.