Motor Bearings-Mainly Deep Groove Ball Bearings or Sliding Bearings in Hollow Cup Motors
- Share
- Issue Time
- Oct 25,2024
Summary
The most commonly used hollow cup motors and torque motors in humanoid robots. Motors can be classified into servo motors and stepper motors according to the control method. Motors can be classified into DC motors and AC motors according to the drive method.
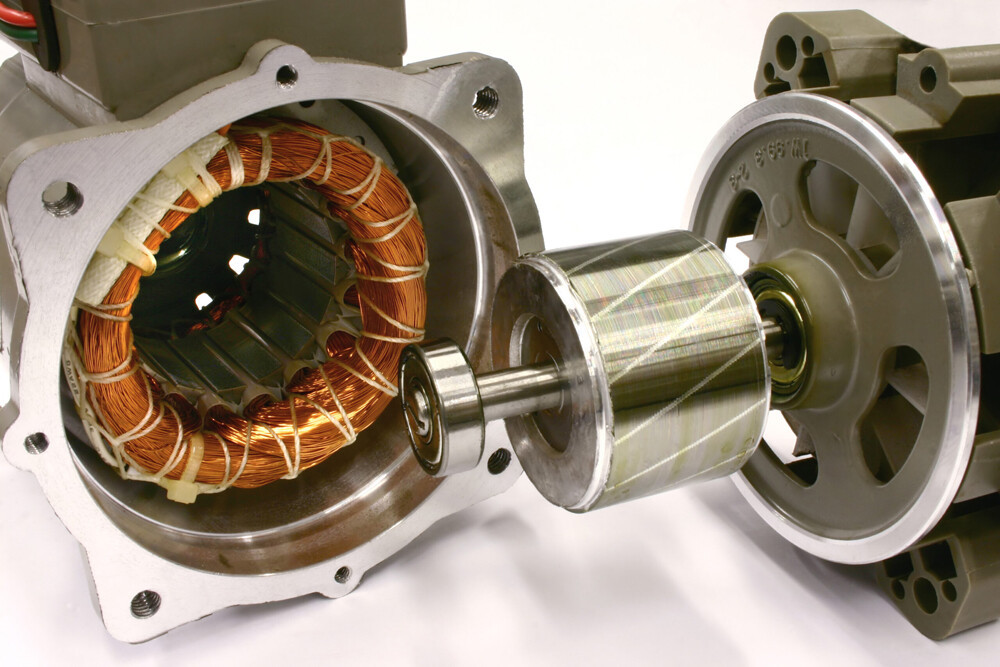
Motor Bearings-Mainly Deep Groove Ball Bearings or Sliding Bearings in Hollow Cup Motors
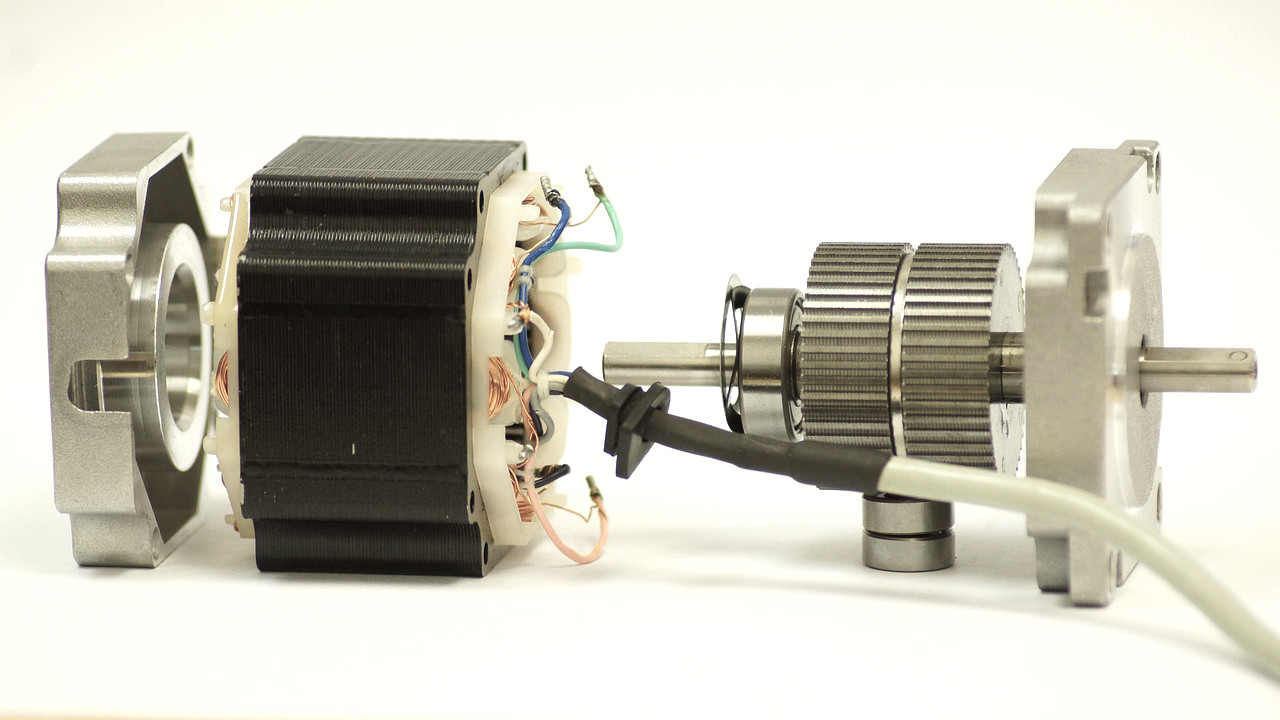
Mainly deep groove ball bearings or sliding bearings in hollow cup motors
The most commonly used hollow cup motors and torque motors in humanoid robots. According to the control method, motors can be classified into servo motors and stepper motors. Motors can be classified into DC and AC motors according to the drive method.
DC motors, according to the coil type, can be divided into iron core motors and hollow cup motors; according to the commutation method, they can be divided into brushed motors and brushless motors. Tesla Optimus robot contains 28 frameless torque motors and 12 hollow cup motors, and the proportion of motors in the overall value is as high as 28%. The hollow cup motor is a micro servo motor. It can use permanent magnets to generate magnetic fields to achieve a DC power supply.
The difference from traditional motors is that hollow cup motors use iron-coreless rotors. The structure of the coreless rotor gives the hollow cup motor the following advantages:
(1) The weight is greatly reduced, thereby reducing the motor's rotational inertia;
(2) The power loss caused by the eddy current formed by the iron core is eliminated;
(3) The mechanical energy loss of the rotor itself is reduced. The motor used in the dexterous hand of the humanoid robot is a hollow cup motor.
The dexterous hand of the Tesla humanoid robot Optimus adopts the classic 6-motor drive solution, that is, it consists of a hollow cup motor + driver + reducer + encoder. The thumb is driven by dual motors for bending and lateral swing, and the other four fingers are driven by one motor each.
Hollow cup motors mainly use deep groove ball bearings or sliding bearings. Taking the hollow cup motor products of Mingzhi Electric as an example, the brushed hollow cup motor has two sliding bearings, and the cost and technical difficulty are lower than rolling bearings; the brushless hollow cup motor has two ball bearings, usually deep groove ball bearings, which have the characteristics of high stability, high precision, low friction, etc., and the technology is relatively mature in China.
A frameless torque motor is a frameless permanent magnet motor that is measured by output torque and does not contain a bearing structure. The principle of a frameless torque motor is the same as that of a traditional permanent magnet motor, and the main difference lies in the structure: a frameless torque motor has no shaft, bearings, housing, or end caps, and only two parts: the rotor and the stator. The rotor is usually an internal component, consisting of a rotating steel ring assembly with permanent magnets, which is directly mounted on the machine shaft; the stator is an external component, with steel sheets and copper windings wrapped around the outside of the gear to generate electromagnetic forces that cling tightly to the machine housing.